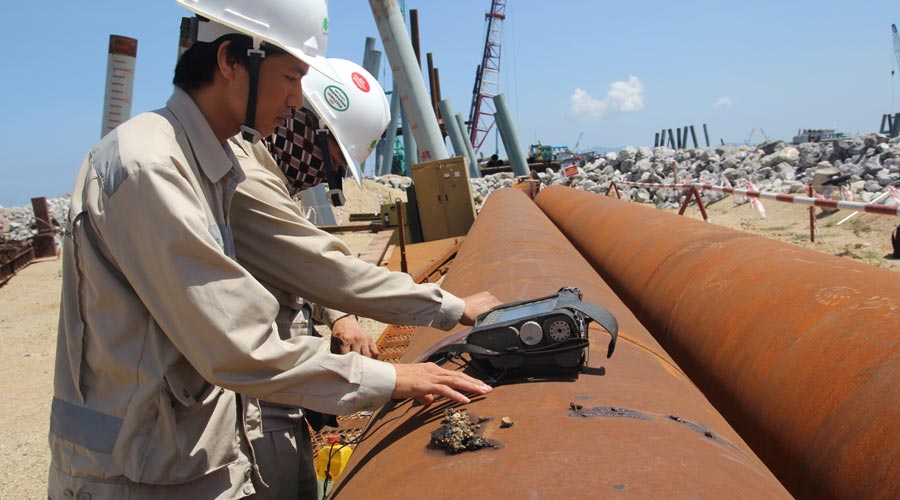
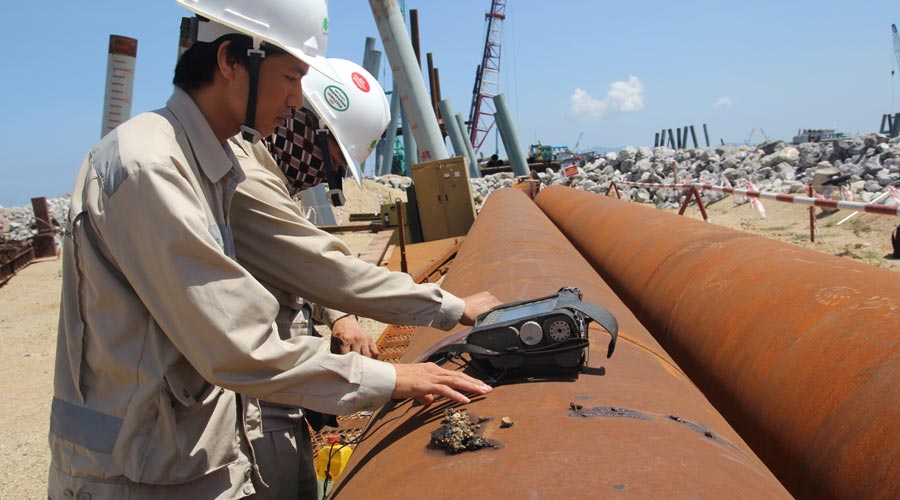
NDT application in manufacturing & installation processes help ensure:
- High levels of quality, while increasing the product safety and compliance
- Low prices by reducing waste product, material and workforce preservation
- Improvement of prestige and competitiveness in the market
NDT application in operational processes allow clients to:
- Ensure the safety of operating systems
- Reduce and save on maintenance costs
- Reduce amount of time spent on plant shutdowns for maintenance purposes
Our
NDT Offer
At Apave we provide NDT services with 3 main techniques:
- Conventional NDT Services
- Specialist NDT Services (Advanced NDT)
- Other Related Services
While conventional NDT methods are currently the main inspection methods for new construction projects, new manufacturing platforms and manufacturing phases, advanced NDT methods are very useful and effective during the operation phase especially for corrosion monitoring. In addition, related services increase efficiency and reduce costs for clients, as is the case with NDT using rope access which results in cost-savings realted to scaffolding materials.
Conventional
NDT Services
- Visual Inspection Services (GVI and CVI)
- Radiography, Gamma/X-Ray (RT)
- Ultrasonic Testing (UT) Services
- Dye Penetrant Testing (DPI - PT)
- Magnetic Particle Testing (MPI - MT)
- Eddy-Current Testing Services (ECT)
- Vacuum box welds testing (LT)
- Infrared Thermography
Advanced
NDT Services
Corrosion mapping
Corrosion mapping is a technique which uses ultrasound to detect and identify damage to materials by mapping their thickness, which is then visually displayed as a graphic image.
- Automated Ultrasonic (AUT) Corrosion Mapping - RMS
- High speed remote access ultrasonic (UT) crawler
- Scorpion Tank Crawler
- Hydro-form - Phased Array Corrosion Mapping
- Flexoform– Phased Array Corrosion Mapping for pipe elbows and small diameter piping
- 3D Laser Scanning for corrosion and mechanical damage assessment
- MFL - Tank floor corrosion Mapping (MFL)
- Pulsed Eddy Current – PEC
- Pulsed Eddy Current Array - PECA and PECA HR
- EMAT - Electro Magnetic Acoustic Transducers
- AE – Acoustic Emission
- Digital and Real time radiography
Weld inspection
Welds may be tested using a variety of NDT techniques, allowing you to determine the integrity of welds - an extremely common component in the industrial sector.
- PAUT and TOFD manual and automated weld inspection services
- ACFM – Alternating Current field measurement
- Eddy Current Array (ECA) Weld and Stress Corrosion Cracking Inspections
- Close proximity Radiography: Apave can supply close proximity equipment such as SAFERAD or SCAR that allows a number of units to be operated simultaneously in a small area, providing very high production rates. Barrier sizes are greatly reduced and easily manageable.
Advanced Tube Inspection
Advanced tube inspections allow you to continuously monitor the state of all types of tubes to determine their integrity and identify corrosion or other damages inside the tube, without the need to open it.
- Remote Field Technology (RFT)
- Near Field Testing/Near Field Array (NFT/NFA)
- Magnetic Flux Leakage (MFL)
- Eddy Current Testing/Eddy Current Array (ECT/ECA)
- Internal Rotary Inspection System (IRIS)
Other
related services
Materials In-Service Inspection services
- Positive Material Identification (PMI) Testing Services - Laser Based and X-Ray Based
- Material examination including replica
- Hardness testing
Rope Access Services
- Painting, Blasting
- Electrical Installation and maintenance
- Lifting gear surveys
- Concrete inspection/ surveys
- Fire & gas maintenance and survey
- Communication Towers Inspection and Maintenance
- Wind Turbines maintenance
- Confined Space entry
- Deck net/ web net
- Any task not accessible by usual means
Nghi Son refinery
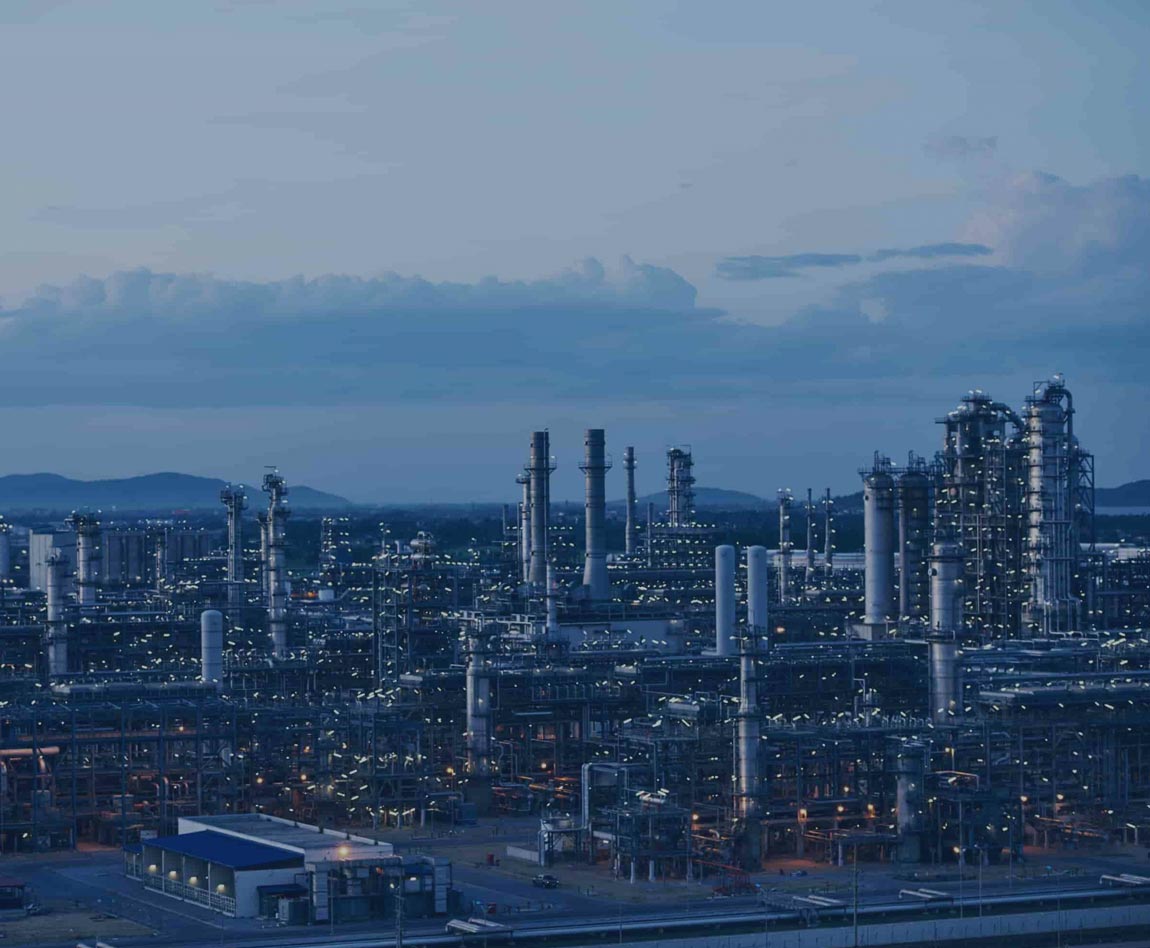
Why Choose
Apave Vietnam?
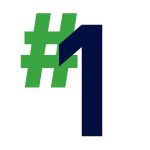
Unique experience of over 150 years
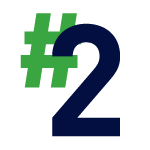
Multidisciplinary approach to your needs
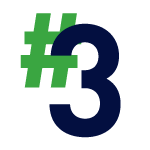
Ability to support you in your transformation projects
Our
Client references